For a long time the solar industry - particularly the residential solar industry - has portrayed our systems as "maintenance free". "Clean the panels when they get dirty, but otherwise you are good to go," is a common conversation between an installer and their client. And certainly given the ever-improving warranties being offered by top-line manufacturers, that claim didn't seem so far-fetched. But lately I've seen some things that have caused me to rethink that whole conception of maintenance-free solar systems. Here's my take...
Old Thinking...
My old thinking - that these systems really did not require maintenance over a 20-year lifetime - was predicated on more than wishful thinking. After all, we used only the very best components: LG solar panels, Enphase microinverters, racking from Everest and Unirac, Polaris connectors instead of wire nuts, etc. We built our systems with care, using well-trained people, including those who were NABCEP certified, and we went above and beyond all code requirements.
What I have discovered recently, in servicing a couple of older systems, is that it isn't the components people worry about failing like the panels or the microinverters, that cause the problems. We have never had an LG panel fail, and since Enphase moved to the IQ series of microinverters we have had exactly one microinverter fail - one!
No, that has not been the problem, it is the little stuff that is taking systems down.
What I've Seen...
Before I can talk about how things have failed, let me show you how things start out.
On the right you see a rail-mounted junction box on the roof. In here we connect the Enphase IQ-cabling from the microinverters to THHN-2 wire for the run from the roof to the building-mounted combiner box. (If you look to the right, your can see black marks on the racking bolts - we mark them with a sharpie after they have been torqued.) We have a grounding bushing on the incoming conduit, and all of the connections are made with Polaris connectors instead of outdoor-rated wire nuts. Why the Polaris? Because you can do a pull test on your connection: when the wires are screwed in you can pull on them to make certain that they are secure, something you simply cannot do with a wire nut.
Put simply, it is the best connection method of which I'm aware and so that is why we use them, even though they cost 50 times as much as that wire nut. But here's the thing - they aren't foolproof either.
|
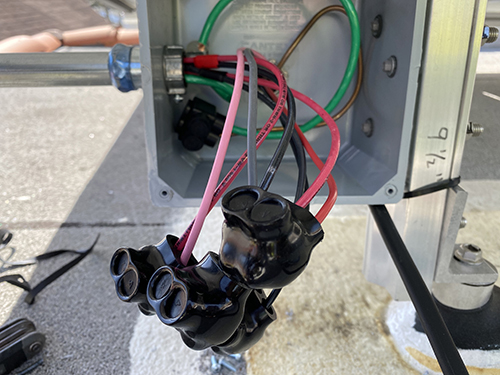
|
We got an email from the Enphase Enlighten monitoring system alerting us to a client whose system had gone offline. That system had a fused disconnect and I fully expected to find a blown fuse. Nope fuses were fine, and the breaker hadn't tripped either. Time to go on the roof and check out the junction box - and here's what I found...
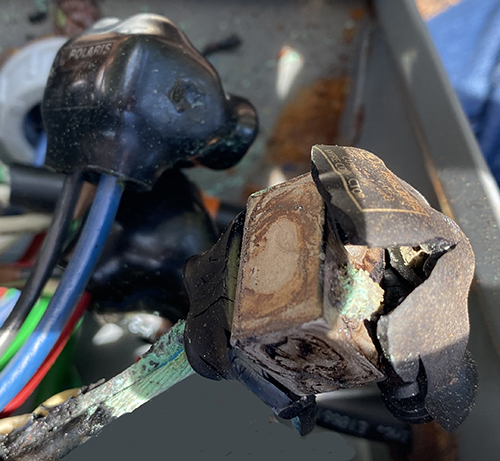
|
What on earth? The Polaris in the foreground has failed completely, but why? The Polaris behind it looks like the day it was installed, so why did the other one literally melt away? Mind you, this wasn't a case of something shorting out - neither the fuses nor the breaker tripped.
There are two wires being joined there, a 12 gauge from the Enphase cable and a 10 gauge for the run off the roof. The #10 is still securely held in what is left of the Polaris, but the #12 has broken off - which is why the system had failed. But why?
My best answer - speculative of course because I didn't see it happen - is that perhaps the #12 was not as securely under the screw as it should have been, and over the course of the nine years that it was in service, with the daily heating and cooling, it continued to loosen, until the resistance of the connection increased, causing it to heat, melting insulation on the wires and on the Polaris, until the wire broke.
|
What could have prevented this failure? Well, as mentioned, this system performed just fine for nine years before failing. What if those connections had been checked around Year 5? If, as I surmise, the connection was loosening, an inspection might have caught that and a simple re-tightening would have cured the problem before the failure could occur.
Now this is only one failure out of a multitude of systems using the same components, so it is fair to say that this is low-probability event. But we have seen other, similar issues including a performance meter that failed, and a line-side tap that loosened, over heated, and failed.
The bottom line is that we are re-thinking how we approach maintenance for resi solar. I would be interested to hear other folks thoughts about this, so please leave us a comment and tell us about your experiences. Hopefully we can all learn something about how to make our systems better, if not, "maintenance free."
|